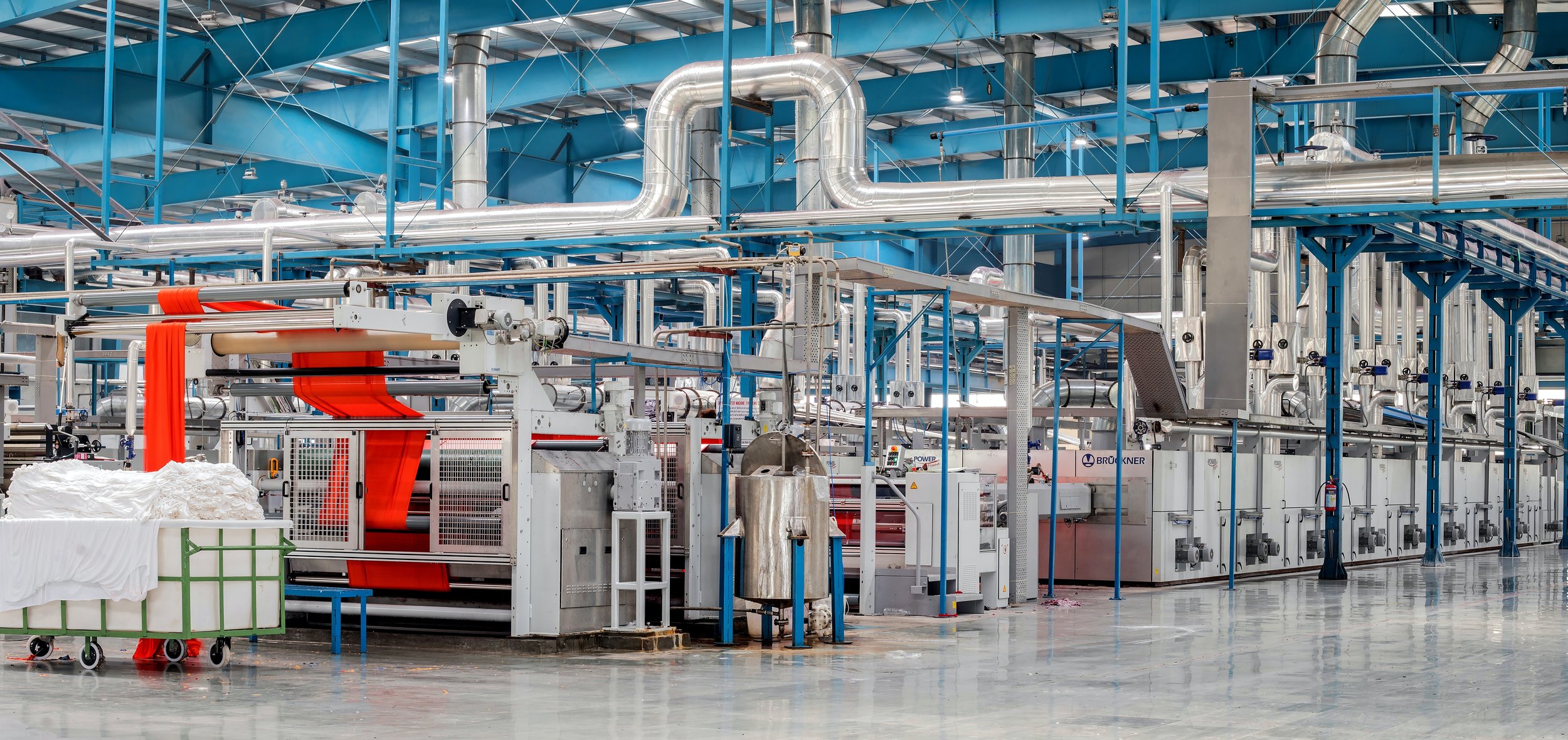
Stainless Steel Bearings
Maximum performance, Minimal Space
MAC offers high-precision ball bearings with a bore of 1 to 35 millimeters and an outer diameter of 3 to 47 millimeters perform critically important functions all from the power of their minute sizes.
Perfect performance demands material of the highest quality. The professional selection of raw materials, parts and components enables us to constantly provide our customers with consistently high quality. t ball bearings are made of chrome steel (100Cr6), stainless steel (X65Cr13 or X105CrMo17), or high corrosion resistant steel (X30CrMoN15-1). Similar load ratings are achieved for all these steel types following ISO and AFBMA standards. It has always been our policy to choose the most advanced material available – for example the alloy Cronidur 30 or XD15. It uses the constituent’s nitrogen, carbon, chrome and molybdenum in a new type of alloy composition. Ceramic balls, e.g. for hybrid ball bearings with steel rings, can be used in addition to exceed the boundary conditions of ball bearing applications.
Criteria for Selection
Hardness
Material cleanliness
Fatigue resistance
Workability
Dimensional stability
Corrosion resistance
Wear resistance
Temperature range and capability
Stainless Steel Types
X65Cr13 Bearing Steel SS (X65Cr13)
In the 1980s the demand for stainless steel miniature bearings with specific low noise behavior was growing significantly. In 1989 MAC introduced to their customer X65Cr13 as replacement to X105CrMo17. Today it is the most commonly used bearing steel for miniature ball bearings.
X30CrMoN15-1 (Cronidur)
Bearing Steel Cronidur. In the mid-90s, a new nitride bearing steel was introduced. The superior features of high corrosion resistance and wear resistance are achieved by partial substitution of carbon by nitrogen. Its low carbon content provides additionally excellent behavior at mixed friction.
440C Bearing Steel S (X105CrMo17)
Major advances in steel production have occurred beginning in the 1950s by the introduction of vacuum-melting procedures. Alloy steels with high chromium content, greater than 12 percent, are considered corrosion resistant. However, although the chromium forms a passive chromium-oxide layer at the surface that provides substantial protection, it is not inert and these alloys will corrode in hostile environments. Long proven heritage in aerospace applications is a further advantage of 440C.